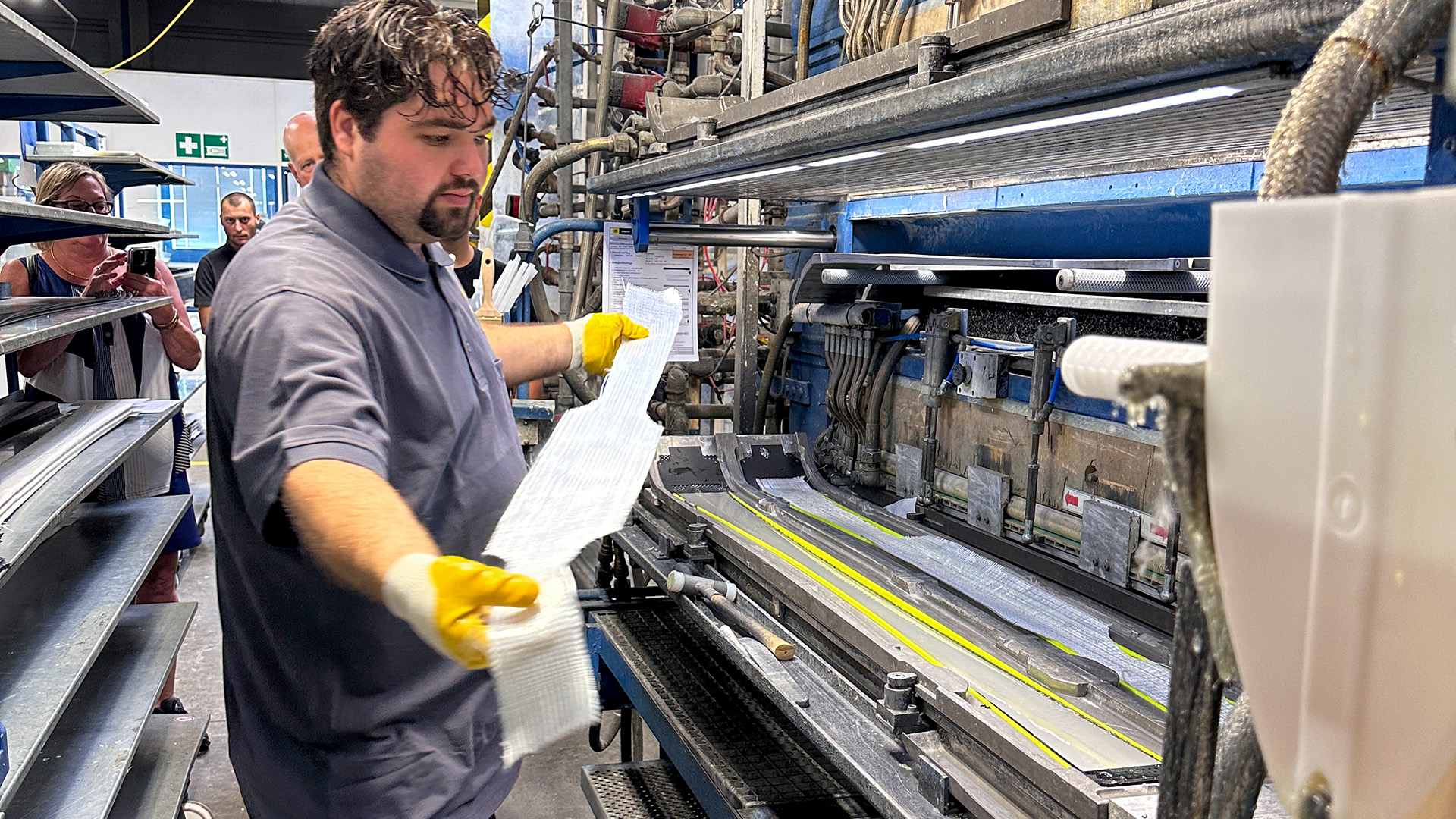
In the fall, while on a tour of the Völkl factory in Straubing, Germany, I only shut down the manufacturing line once. Accidentally.
I think guide Maximilian was being polite when he explained that the invisible laser beams keep one safe from robotic arms, conveyors and spinning things. It’s not the first time my curiosity, and my camera, have landed me in trouble. But with a recent €3-million investment in robots, it was pretty obvious the lasers were protection from me, more than for me.
In total, 430 employees work around the clock in three shifts. Despite the impressive automation, there is still far more hand-made production than one would think in the modern, 16,000-square-metre plant. For instance, only eight Völkl employees are allowed to hand-bend ski tips—and only two on the race skis. Somehow 1,800 pairs get out the door every day.
From one impeccably neat and clean room to the next, smells range from wood cores to epoxies to topsheet silk screening to base grinding. Some models can contain up to 65 different pieces. Keeping my hands in my pockets, I watched as layers upon layers were sandwiched with dripping resin into the press before everything was popped into the 120°C oven for 23 minutes. Preproduction to completed ski takes three weeks.
In our ski world, where lots of companies and ski areas are marking a 50th or maybe 60th anniversary, it’s quite incredible that Völkl celebrated its 100th year of building precision skis. Germans sure know how to make stuff.
Have you ever skied on a pair of Vöstras? I haven’t either. While patriarch Georg Völkl was a well-established wainwright (a builder of sleighs and wagons) in the 1800s and early 1900s, it was his son, Franz, who decided in 1923 that they should get into the ski biz. Boom! Völkl was out of the starting gate. The ski went under the name of Vöstra for the first 40 years or so before using the family name Völkl—or Voelkl for typewriters without umlauts.
Völkl’s first major win was in 1961. With a Bavarian team. In curling. But its skis were soon winning on race courses and by 1965, with Franz Jr. then in charge, the fairytale Bavarian town of Straubing was laying up 100,000 pairs a year. (A number that increased fourfold by the year 2000.) Meanwhile, in swinging ’60s U.S.A., if you skied on Sears skis (yes, that Sears) you were on a pair of custom-topsheet Völkls.
In 1967, Völkl hit the jackpot with its Zebra ski. Their unique black-and-white stripes stood out in a liftline of otherwise placid cosmetics by Head, Kneissl, Fischer and the only ski manufacturer I can think of that’s been around longer than a century, Rossignol.
Five years later the all-metal, bold-yellow striped Renntiger was winning races; its rebirth in 2005, the Race Tiger, was equally explosive. See inset photo, left.
In 1972, Völkl introduced the world’s first 100 percent plastic tennis racquet, cleverly named Zebra. Snowboards, nordic skis and golf gear all followed. Neon Völkl onesies with Princess Di shoulder pads of the late ’80s still sell fast at Value Village.
But it’s always been (mostly) about skis. The 1980s saw the P-Series with the P9 under world champ Maria Walliser’s feet. By 1992, the company was no longer headed by a Völkl surname and the skis were no longer made in “West Germany,” just Germany. At some point, someone said “carving” and German skiers realized no one does it better. Völkl managed to keep the “Carver” trademark rights in Europe until 2015. Around the same time the V-Ski Freeride and Freestyle and a new millennium of New School blossomed. The Mantra was born in 2005, five iterations later…and I’ve run out of space here.
Now, what’s in the works? For 2025, watch for the new Peregrine 82. Named after, not surprisingly, the world’s fastest bird. With an integrated iPT binding and fast World Cup 4504 base, Völkl promises a new definition of playfulness and versatility.
And another 100 years of fun.
